A Cost saving Arrangement for your Steam Processing Operation
Have you ever thought about why a technical consultant suggests buying a high-pressure boiler? It then reduces the pressure by using the pressure reduction valve (PRV) to the required level as per the process requirement. In general observation, it seems like a cost increasing step since you need to buy an extra device (Pressure Reduction System) and other extra fittings to install in the steam line. But it is not so!
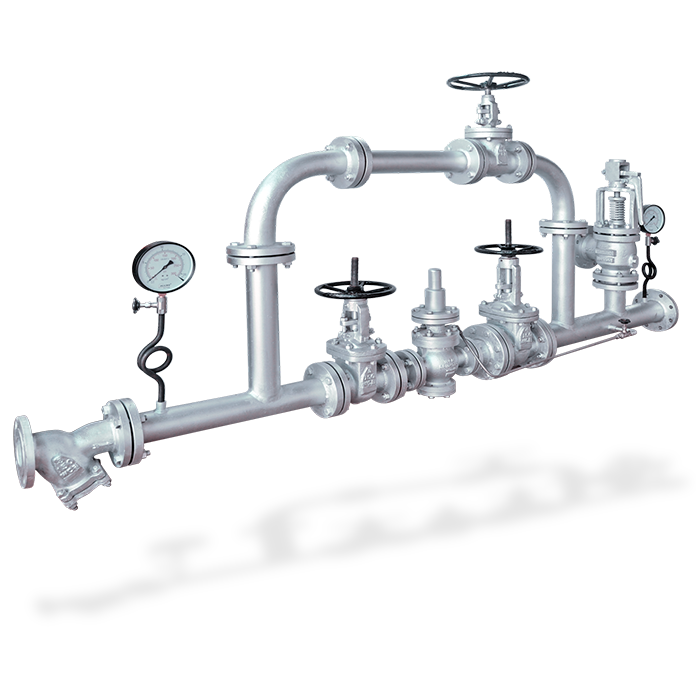
Let’s dig a little deeper, whether using a PRS is practically feasible or not.
Steam generation at high pressure helps reduce the initial investment cost. At high pressure, the specific volume of steam is lower than at low pressure, which means a smaller diameter pipe is required to carry the steam. This reduces the cost associated with piping, leading to a reduction in the overall initial investment cost.
High-pressure steam generation also results in relatively less carryover and provides better-quality steam. At low pressure, carryover is more likely to occur, which can affect steam purity. By using a high-pressure boiler, the steam can be utilized in different applications at varying pressures with the help of a Pressure Reducing Valve (PRV). Additionally, high-pressure steam boilers offer flexibility for variable loads.
A sudden increase in load reduces the boiler pressure and increases carryover, leading to higher moisture content in the steam. The PRV helps eliminate this issue by maintaining a constant pressure in the boiler, ensuring stable steam quality. Furthermore, generating steam at high pressure is relatively more cost-effective than using a low-pressure boiler, as it reduces fuel consumption.
Now that we have a brief understanding of the benefits of a PRV, it’s important to note how it functions. Any porous plug or orifice valve that reduces the cross-sectional area of the flow can act as a pressure reducer. However, during fluctuating loads, the outlet pressure of such valves will also fluctuate, which is undesirable. To eliminate this issue, a PRV is used, ensuring constant pressure even during variable loading conditions.
Let's look more closely at what the technical data suggests
A pressure reducing valve is a regulating valve that maintains the steam pressure at the outlet at a certain fixed, prescribed level that is lower than the inlet pressure. The PRV not only reduces the pressure but also controls the flow by load fluctuation dynamically. Therefore, using the change of state of steam caused by adiabatic steam expansion, not only the pressure changes but the temperature, specific volume, and latent heat also change.
Effects caused by PRS
1. Quality improved of steam: Pressure reduction is the use of adiabatic steam expansion. Since the latent heat of steam changes as pressure changes, dryness fraction increases.
For example: If the saturated steam at pressure is 10 kg/cm2 with a 95% dryness fraction is reduced to 3 kg/cm2.
Enthalpy of steam at inlet of PRS = 181.2 + 0.95*481.8 = 638.91 kcal/kg
And the dryness fraction at the outlet = (638.91-133.4)/516.9 = 0.977= 97.7%
Now we can see a 2.7% increment in the dryness fraction. which simply means less condensate will form inside the pipe and more steam will reach the process.
2. Reduction in piping cost. : As mentioned above, the PRV allows the generation of steam at high pressure, and at high pressure the density of steam is high, which requires less space, so high pressure steam can be carried in a small diameter pipe as compared to low pressure steam. Considering the above example,
The density of steam at 10 kg/cm2 = 5.049 kg/m3
Velocity of steam in pipe = 30 m/s
Capacity of boiler = 2000 kg/hr
Then, the pipe required to carry the high pressure (10 kg/cm2) steam at a rate of 2000 kg/hr is,
Steam capacity (kg/s) = density * area velocity 2000/3600 = 5.0490.785*D2 * 30
Inner diameter D = 68.38 mm.
And pipe required to carry the low pressure (3 kg/cm2) steam at the rate of 2000 kg/hr is,
The density of steam = 1.622 kg/m3
Velocity of steam = 30 m/s
2000/3600 = 1.6220.785D2 *30
D = 120.4 mm
So, by using the PRV before the process, a large piping coat can be saved since a lower diameter pipe will be required.
3. Reduced Carry Over: Low pressure boilers are more prone to carryover. The PRS reduces the boiler carry over by allowing us to generate the steam at high pressure and ensure the contaminants free steam reaches the process. Since carry over reduces the life of the valves, strainers, and pipes, so PRS also improves the life of the system indirectly.
4. Even heating conditions: PRV keeps the outlet pressure constant and stabilizes the heating conditions, which ensures uniform productivity by maintaining the constant temperature.
5. Single boiler for different applications: With the help of PRV, a single boiler of high pressure can be used for different applications at different pressures.
For example, if a steam process unit has three different operations in which steam is required at 5 kg/cm2 pressure, 6 kg/cm2, and 4 kg/cm2 with a capacity of 2 TPH, then in this case, instead of three different boilers, you can choose a single boiler of 6 TPH capacity and pressure greater than 6 kg/cm2.
Precautions During PRV Installation: It is also important for you to know whether the installation of PRV is appropriate or not. Since an improper location of PRV may cause you losses and would not have any benefits. Some of the basic factors you should take into consideration are as follows:
A PRS should be installed just before the process and not in the main steam line.
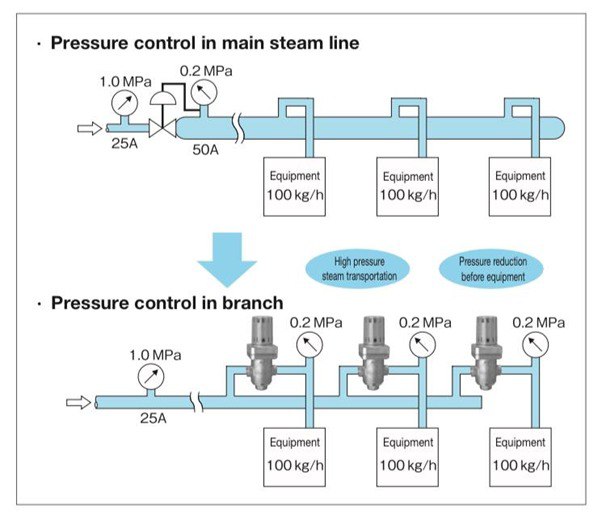
Pressure control in main steam line
For larger pressure reduction, a combination of PRS should be used for the best and most controlled operation.
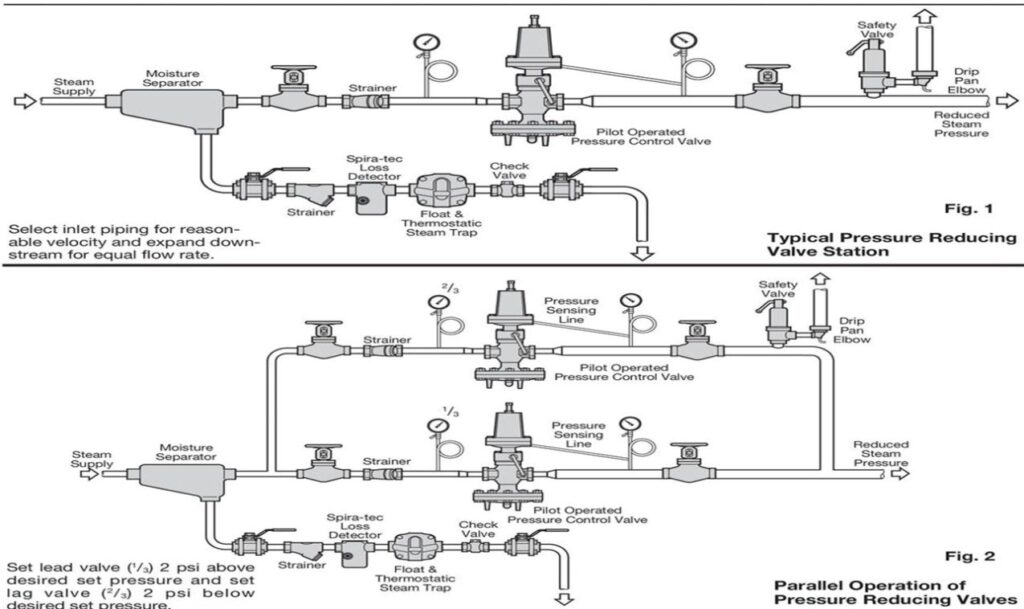
Have No Idea Where to start with?
We at Thermodyne Engineering System provide the most energy efficient steam energy solutions which are best suited to your process. Our team of experts is always at a phone call distance to help you make your process energy efficient and reduce the steam energy loss by optimising the operation. Contact Us to increase your boiler system efficiency and reduce the operating cost.
FAQs Related to Pressure Reduction Systems (PRS)
A PRS is an arrangement of valves and components designed to reduce high-pressure steam from a boiler to a lower pressure required for specific industrial processes while maintaining consistent flow and pressure.
High-pressure steam reduces initial investment costs by enabling smaller diameter pipes, minimizes carryover, and allows flexibility for multiple applications with varying pressure requirements.
A PRV regulates steam flow and reduces its pressure dynamically, ensuring constant outlet pressure even during load fluctuations.
Improved steam quality (higher dryness fraction).
Reduced piping costs due to smaller pipe diameters.
Minimized carryover, enhancing equipment life.
Consistent heating conditions for uniform productivity.
Yes, with a PRS, a single high-pressure boiler can supply steam at varying pressures for different process requirements, eliminating the need for multiple boilers.
Yes, generating steam at high pressure is more fuel-efficient, and the PRS ensures optimal energy utilization by reducing losses in the system.
Install the PRS near the process equipment, not on the main steam line.
Use multiple PRVs for larger pressure reductions to maintain control and efficiency.
By reducing pressure through adiabatic expansion, the dryness fraction of the steam increases, resulting in less condensate formation and better-quality steam reaching the process.
The inlet and outlet pressures, flow rate, and desired accuracy of pressure reduction are key factors in sizing a PRS.
By minimizing carryover and ensuring contaminant-free steam, it reduces wear and tear on valves, strainers, and pipes, extending their lifespan and lowering maintenance expenses.