In this fast-paced industrial world, where energy costs are skyrocketing and environmental regulations are tightening, optimizing boiler efficiency isn’t just about saving money—it’s about staying ahead of the game. Think of it like fine-tuning a high-performance car, every little tweak can make a big difference. In addition to lowering their fuel costs, businesses can increase productivity and ultimately market competitiveness by using smart approaches. From selecting the ideal boiler design to putting in place intelligent energy-saving controls, we’ll explore the best strategies to increase your boiler’s efficiency.
1- Selecting the right Boiler
Selecting the Right Boiler Design :
- Fire Tube Boilers are ideal for low to medium pressure (up to 25 bar), suitable for small to medium industries. Water Tube Boilers are an ideal choice for high-pressure applications (above 25 bar), and are generally used in large industrial setups.
- Electric Boilers are a great option for low capacity, low pressure and clean energy requirements.
Choosing the Right Boiler Capacity :
- Consider peak demand and variable steam loads to calculate the right capacity of the boiler. Always calculate the capacity based on the gross load of the boiler, keeping in account the efficiency.
Selecting the Right Pressure Rating :
- Boilers are rated based on operating pressure. Choosing the correct pressure depends on your application. Choose a pressure rating 10–15% higher than your actual requirement to ensure safety and efficiency.
Determining Steam Holding Capacity :
- Different boiler fuels impact efficiency and operating costs. For example, Natural gas makes a very clean fuel and is a very efficient system (Up to 95%), but people often select wood or coal fired boilers as they make much cheaper fuel options but the thermal efficiency is usually 80 to 85%. Selecting the right fuel as per availability, cost, thermal efficiency and government regulations is very crucial. Consider dual-fuel boilers for flexibility in fluctuating fuel costs.
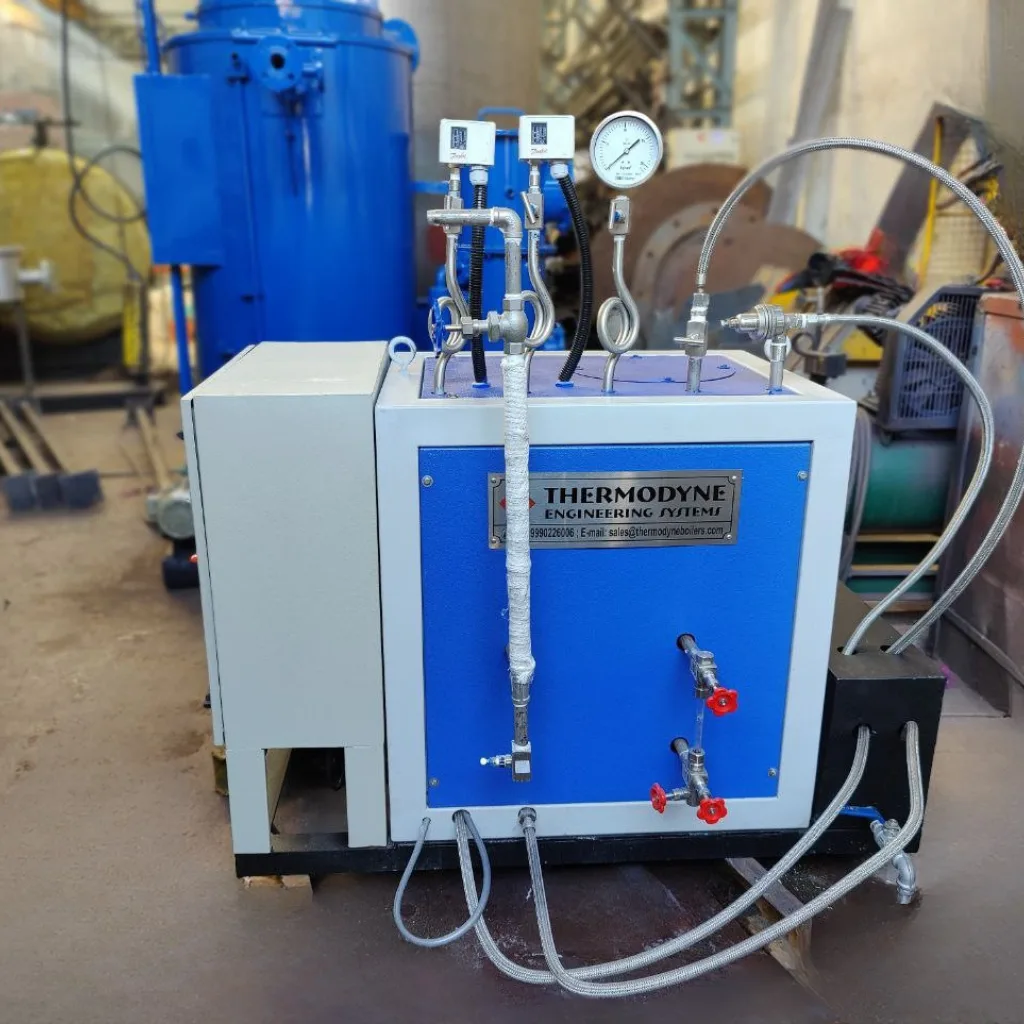
Electric steam Boiler
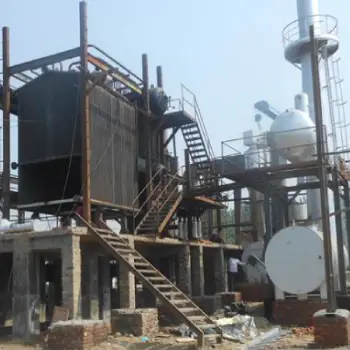
Water Tube Boiler
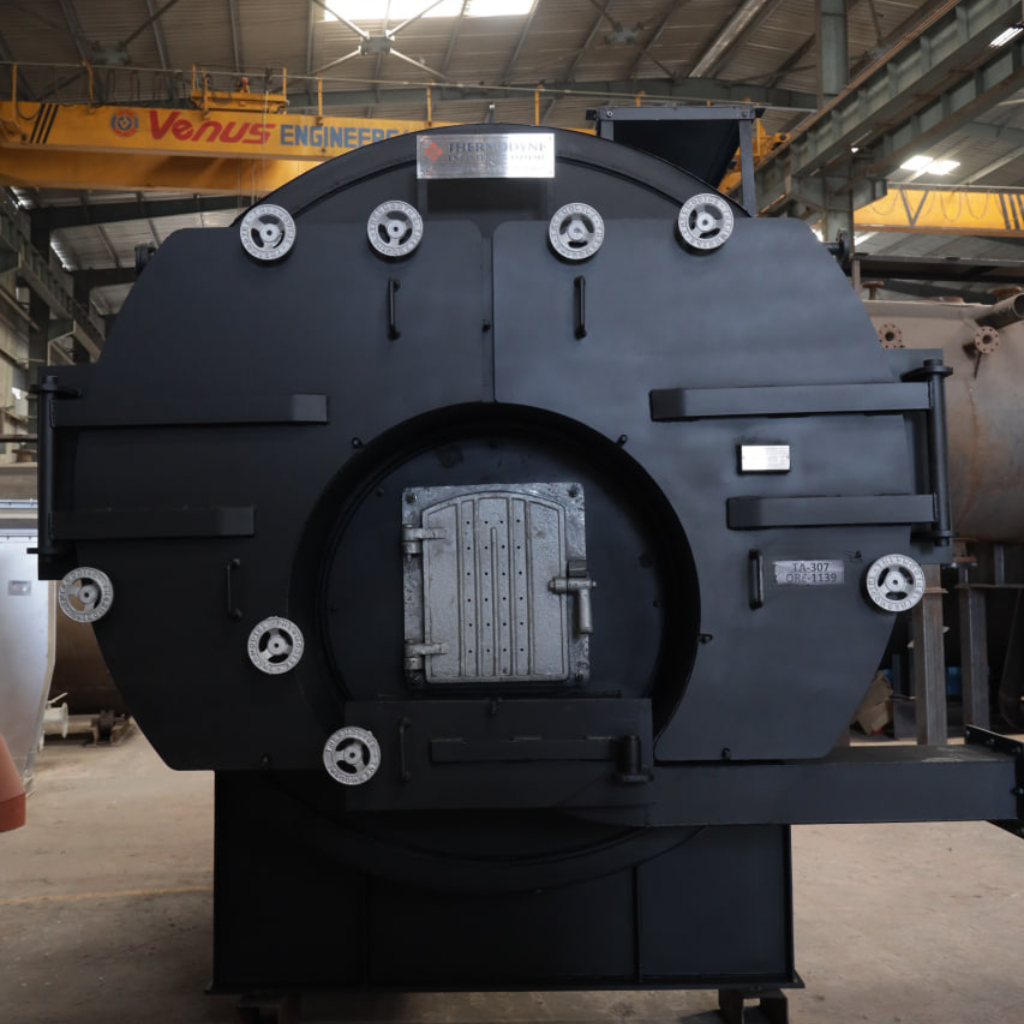
Fire Tube Boiler
2- Conduct Regular Maintenance
Regular maintenance is essential for a healthy running of a boiler. Routine inspections including cleanings and calibrations ensure that boiler operates efficiently.
- Clean the waterside and fireside: Deposition of scale and soot over time results in increase of boiler load as its accumulation over time reduces the quality of heat transfer taking place. This accumulation may result in expensive repairs and reduction in efficiency. Energy savings and improved heat transfer are guaranteed when these areas are cleaned.
- Look for leaks and corrosion: Leaks, rust, or corrosion can cause energy losses and damage the boiler system. Visual inspection of steam lines and pipelines is easy to conduct inhouse.
- Check Safety Controls: Ensure all safety controls, valves and instruments are functioning correctly and they are properly calibrated. These safety instruments and gauges form an essential part of any boiler system.
3- Optimize Combustion Efficiency
Efficient combustion plays a vital role in achieving optimal boiler performance:
- Air-Fuel Ratio: Properly adjust the air-fuel ratio to ensure complete combustion while minimizing excess air. Excess air can lead to energy wastage and reduced efficiency.
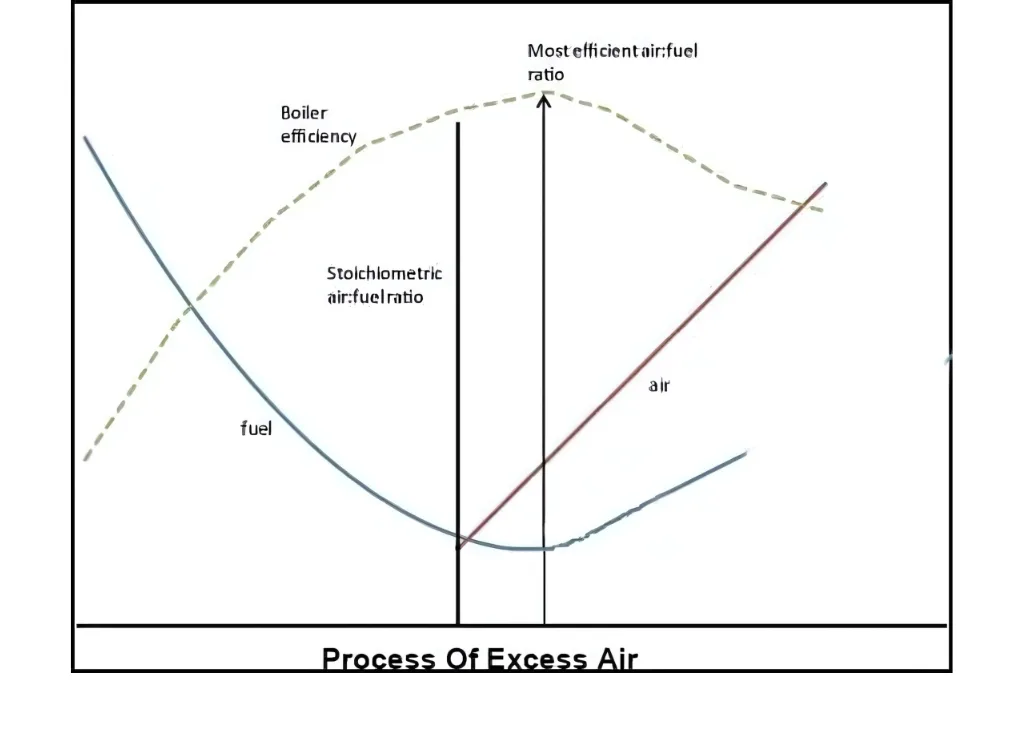
- Use Flue Gas Analyzers: Regularly monitor oxygen and carbon dioxide levels to maintain optimal combustion conditions. Flue gas should consist of CO2 and little to no CO for best results which makes sure that the combustion is happening well in the system.Very low O2 levels results in incomplete combustion and high levels of CO in the flue gas and unburnt fuel emissions. Higher levels of O2 indicate more than required ambient air which cause heat loss thus causing energy wastage.
For fuels that are used with burners like PNG, LPG, Oil, HSD, etc.
- Install Parallel Positioning Burner Controls: These systems optimize fuel-air mixing for better efficiency. Parallel positioning systems use motorized actuators (servos) to control the fuel valve and the air damper to optimize combustion process
- Calibration of burner: Tune the burner more frequently to account for seasonal changes in air temperature, ensuring optimal combustion conditions.
For solid fuels like coal, wood, briquettes, biomass, rice husk, etc.
- Variable Frequency Drives (VFDs): Use VFDs to adjust fan speeds and fuel flow according to load requirements.
4- Implement Energy-Saving Controls
Integrating smart controls can further enhance your boiler efficiency. Integrating energy-saving controls can further enhance boiler efficiency. Install programmable thermostats, time switches, or advanced control systems that allow you to manage and adjust boiler settings based on occupancy patterns or demand. These controls enable you to optimize temperature settings, reduce standby losses, and prevent unnecessary energy consumption during periods of low demand. Utilizing smart controls ensures that your boiler operates efficiently and minimizes energy waste.
5- Reducing Heat Losses
Reducing heat losses in a boiler system is crucial and the simplest way to drastically improve thermal efficiency of a boiler system. It helps maintain optimal steam generation while minimizing environmental impact by reducing emissions.
- Heat Recovery Systems: Implement heat recovery systems like economizers and Air pre-heaters to capture and reuse waste heat. Economizers are used to preheat feedwater, and Air-preheaters are used to preheat the combustion air, this brings in the wasted heat back into the system.
- Recovering condensate: The condensate recovery system is a low cost, high returns solution for processes that utilizes boiler steam for indirect heating. The Condensate recovery system collects and reuses the hot condensate from processes and returns it to the boiler feedwater tank, reducing energy loss and water consumption.
- Enhance Insulation: Insulate pipes, valves, and boiler surfaces to minimize heat loss. Proper insulation can significantly reduce energy wastage.
6- Opt for Regular Boiler Efficiency Testing
Periodic efficiency testing allows you to assess and monitor your boiler’s performance accurately:
- Combustion Efficiency Tests: Conduct tests to evaluate energy utilization and emissions.
- Stack Temperature Measurements: Lowering stack temperature can improve efficiency by reducing heat loss.
- Flue Gas Analysis: Use data from flue gas analysis to identify areas for improvement and validate efficiency-enhancing measures.
7- Train and Educate Staff
Well-trained staff are crucial for maintaining and optimizing boiler efficiency:
- Comprehensive Training: Provide comprehensive training to your boiler operators, ensuring they understand the system’s operation, maintenance requirements, and efficiency optimization techniques. Empower your staff to identify and report any issues that may affect boiler performance.
- Energy-Saving Practices: Educate staff about energy-saving practices, combustion optimization, and the importance of regular maintenance.
8- Monitor and Analyze Performance
Implement a system to monitor and analyze boiler performance data regularly:
- Maintaining a Boiler Log sheet: This is a crucial document used to record vital operating parameters such as steam pressure, temperature, fuel consumption, and water levels, helping to monitor performance, detect issues early, and improve efficiency and safety.
- Energy Management Software: Using software based Boiler log sheets or data loggers to track key performance indicators such as fuel consumption, steam production, and stack emissions. These are better for performing data analysis. Analyze data to identify trends, efficiency fluctuations, and potential areas for improvement.
Key takeaways to maximize boiler efficiency
Maximizing boiler efficiency is about ensuring long-term reliability, reducing environmental impact, and improving overall operational performance, while also reducing your operating cost for reducing fuel bills. By implementing these simple measures, industries can achieve significant energy savings while extending the lifespan of their boilers. This not only reduces your fuel cost, but also promotes a more sustainable solution. Small changes, such as fine-tuning the air-fuel ratio or investing in heat recovery systems, can lead to substantial improvements. Start by assessing your current boiler efficiency and take proactive steps toward a more cost-effective and sustainable operation.
Every improvement counts!!
FAQs
Water tube boilers are more efficient than fire tube boilers due to faster steam generation, lower water volume requirements, and better adaptability to fluctuating loads, which reduces energy waste. Fire tube boilers, while simpler and cheaper initially, have slower response times and lower heat transfer efficiency
Yes, electric boilers are a viable alternative to gas or coal-fired boilers in industrial settings. They offer key advantages such as high efficiency (up to 99%), zero emissions, compact design, and enhanced safety by eliminating risks. They are particularly suitable for industries requiring clean operations, such as food processing, pharmaceuticals, and textiles. However, higher electricity costs and dependency on renewable energy for zero-carbon performance may limit their cost-effectiveness compared to fossil fuel boilers in some scenarios
Signs of Inefficient Combustion:
Excessive fuel consumption beyond normal levels.
Smoke or soot formation indicating incomplete combustion.
Carbon monoxide (CO) emissions or hydrocarbon traces in flue gases.
Yellow or unstable flames instead of blue flames.
Unusual noises or vibrations from the burner.
Early Detection Methods:
Use a flue gas analyzer to monitor CO and O₂ levels.
Inspect for soot deposits in the boiler or burner area.
Regularly check the air-to-fuel ratio and burner condition
A Variable Frequency Drive (VFD) improves boiler efficiency by adjusting the motor speed to match load requirements, significantly reducing energy consumption. For example, at 50% boiler load, fan power usage can drop to 1/8th of full-load power, saving electricity and operational costs.
Smart control systems that reduce fuel wastage in industrial boilers include:
Advanced Combustion Control Systems: These optimize the fuel-to-air ratio in real-time using sensors for oxygen, carbon monoxide, and nitrogen oxide, improving efficiency and reducing emissions.
Model-Based Predictive Controls: These use mathematical models to stabilize furnace heat release, adjust fuel supply dynamically, and maximize alternative fuel usage.
Smart Sensors and Remote Monitoring: Enable precise temperature and energy management while allowing remote adjustments to reduce unnecessary fuel consumption
Economizers recover heat from boiler flue gases to preheat feed-water, reducing fuel consumption by up to 20% and improving efficiency. Air-preheaters transfer waste heat to incoming air, enhancing combustion and further lowering energy costs
A condensate recovery system can save 10-30% of the initial heat energy in steam, reducing boiler fuel consumption by up to 20% and cutting water treatment costs significantly. It also improves steam quality and reduces environmental impact, making it a worthwhile investment for industries seeking efficiency and cost savings.
Flue gas analysis helps optimize boiler efficiency by measuring key gases like oxygen (O₂) and carbon monoxide (CO). Here’s how to interpret and act on the results:
Ideal Combustion: Aim for 1–3% excess air and 0–200 ppm CO for efficient fuel usage.
High O₂ Levels: Indicates excess air, leading to heat loss. Adjust the air-to-fuel ratio to reduce waste.
High CO Levels: Suggests incomplete combustion. Improve airflow or check burner performance.
Regular Maintenance: Clean fouled surfaces and calibrate analyzers to ensure accurate readings and efficiency improvements.