Dry Bottom Boilers: Clean and Efficient Industrial Steam Generation
Dry bottom boiler
Dry bottom boiler are a type of boiler that is becoming increasingly popular in industrial settings due to their efficiency and cleanliness. Unlike wet bottom boilers, which collect molten slag in the bottom of the furnace, dry bottom boilers allow the ash and other combustion byproducts to fall to the bottom of the boiler in a dry state. This makes them more efficient and easier to maintain, and it also reduces emissions.
Benefits of Dry Bottom Boilers
- Increased efficiency: Dry bottom boilers can achieve efficiencies of up to 99%, which means that they convert almost all of the fuel they burn into steam. This is significantly higher than the efficiency of wet bottom boilers, which typically achieve efficiencies of around 85%.
- Reduced emissions: Dry bottom boilers produce fewer emissions than wet bottom boilers, including nitrogen oxides (NOx), sulfur dioxide (SO2), and particulate matter (PM). This is because the dry ash can be captured and treated, while the molten slag in wet bottom boilers releases emissions when it cools.
- Easier maintenance: Dry bottom boilers are easier to maintain than wet bottom boilers because there is no need to remove molten slag from the bottom of the furnace. This can save time and money, and it can also extend the life of the boiler.
Applications of Dry Bottom Boilers
Dry bottom boilers are used in a variety of industrial applications, including:
- Power generation: Dry bottom boilers are often used to generate steam for power plants.
- Chemical processing: Dry bottom boilers are used to heat fluids in chemical processing applications.
- Food and beverage production: Dry bottom boilers are used to sterilize food and beverages.
- Pharmaceutical manufacturing: Dry bottom boilers are used to sterilize equipment and products in pharmaceutical manufacturing.
- Textile production: Dry bottom boilers are used to heat water for textile processing.
A dry bottom boiler – The burner fires in the base of the boiler and it warms beneath the water some portion of the boiler. No slag tanks at heater throat zone. The throat range is clear. Base fiery remains drop through the throat to the base powder water containers.
This plan is utilized where the slag dissolving temperature is more noteworthy than the temperature on the heater divider, taking into account generally dry heater divider conditions.
Our Dry Bottom Boiler Model : INTECH BOILER
Checkout our Steam Products: Thermodyne Products
Wet Bottom Boilers: Efficient Steam Generators with Distinctive Features
The wet base boiler is a boiler that contains a wet base heater. It is a sort of boiler utilized for pummeled fuel terminating. In the wet bottom boiler, the base fiery debris is kept in a liquid state and tapped off as a fluid.
Wet bottom boilers, a prevalent type of industrial boiler, are known for their efficient steam generation and distinctive characteristics. Unlike dry bottom boilers, which collect molten slag in the furnace, wet bottom boilers allow ash and other combustion byproducts to form a liquid slag at the bottom of the boiler. This slag is then removed through a slag tap, ensuring efficient operation and minimizing the formation of carryover.
Key Features of Wet Bottom Boilers
- Slag Formation and Removal: Wet bottom boilers facilitate the formation of a liquid slag through specific design features. This slag, composed of ash and other impurities, is denser than water and sinks to the bottom of the furnace. A slag tap is employed to periodically remove the slag, ensuring continuous operation without slag accumulation.
- High Steam Temperatures: Wet bottom boilers typically operate with higher steam temperatures compared to dry bottom boilers. This is because the liquid slag provides better heat transfer, allowing for more efficient steam generation.
- Suitability for High-Ash Fuels: Wet bottom boilers are particularly well-suited for handling high-ash fuels. The slag formation process effectively captures and removes ash, minimizing the risk of slag carryover and subsequent boiler damage.
- Wide Range of Applications: Wet bottom boilers are employed in various industrial applications, including power generation, pulp and paper production, and steel manufacturing. Their high efficiency and adaptability make them a popular choice in these sectors.
A Reliable Steam Generator for Diverse Applications
Wet bottom boilers stand out as efficient steam generators with distinct features. Their ability to form liquid slag, handle high-ash fuels, and operate at high steam temperatures makes them a versatile option for various industrial applications. As the demand for clean and efficient steam generation continues to grow, wet bottom boilers are poised to play an increasingly crucial role in industrial processes.
Also Read: A to Z Boiler Terminology
Wet bottom boiler slag is a term that portrays the liquid state of the fiery debris as it is drawn from the base of the slag-tap or violent wind heaters.
A wet bottom boiler – The burner fires in the base of the boiler and it warms above, at, and underneath the water some portion of the boiler (this is a greatly improved warmth exchange evaporator outline than that of a dry base)
Our Wet Bottom Boiler Model: SAVEMAX BOILER
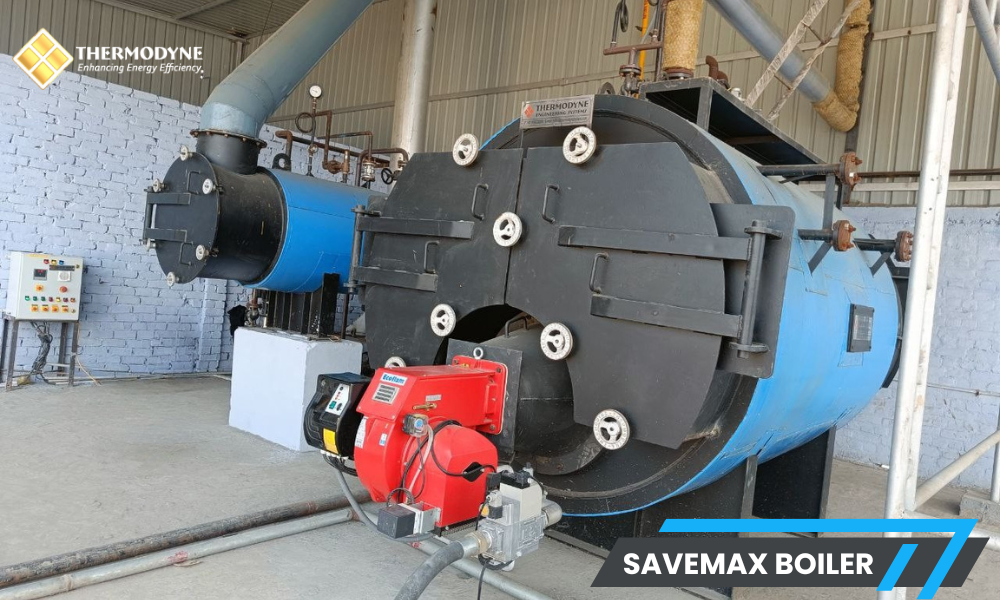
A dry bottom boiler is a type of boiler in which the ash and other combustion byproducts are removed from the bottom of the boiler in a dry state. This is in contrast to a wet bottom boiler, in which the ash and byproducts are removed in a wet state.
Dry bottom boilers have several advantages over wet bottom boilers, including:
They are more efficient, because the ash and byproducts do not cool down the combustion process.
They produce less slag, which can cause problems in wet bottom boilers.
They are easier to maintain, because the ash and byproducts are easier to remove.
Dry bottom boilers have a few disadvantages, including:
They are more expensive to purchase and install.
They require more frequent inspections and maintenance.
They can be more prone to corrosion.
There are two main types of dry bottom boilers:
Pulverized coal boilers: These boilers use pulverized coal as their fuel. The coal is ground into a fine powder and then burned in the boiler.
Fluidized bed boilers: These boilers use a bed of inert material, such as sand or limestone, as their fuel. The fuel is burned in the bed of material, which creates a fluidized bed.
Dry bottom boilers work by burning fuel in a furnace. The heat from the fire is transferred to water, which turns to steam. The steam is then used to generate power or heat.
Dry bottom boilers require regular maintenance to ensure that they operate safely and efficiently. This maintenance includes:
Inspections: The boiler should be inspected regularly for any signs of damage or wear.
Cleaning: The boiler should be cleaned regularly to remove ash and other combustion byproducts.
Repairs: Any damage or wear that is found should be repaired promptly.
Dry bottom boilers can pose a number of safety hazards, including:
Fire: The boiler can catch fire if the fuel is not properly burned.
Explosion: The boiler can explode if the pressure inside the boiler becomes too high.
Burns: The boiler can cause burns if the steam or hot water that is produced is not properly contained.
There are a number of things that can be done to prevent accidents involving dry bottom boilers, including:
Properly training operators: Operators should be properly trained on how to operate and maintain the boiler.
Following safety procedures: All safety procedures should be followed at all times.
Conducting regular inspections: The boiler should be inspected regularly for any signs of damage or wear.
Repairing any damage or wear promptly: Any damage or wear that is found should be repaired promptly.
There are a number of resources available to learn more about dry bottom boilers, including:
Manufacturers’ websites: Manufacturers of dry bottom boilers often have websites that provide information about their products.
Trade associations: There are a number of trade associations that represent the dry bottom boiler industry. These associations often have websites that provide information about the industry.
Government agencies: Government agencies, such as the Occupational Safety and Health Administration (OSHA), often have information about dry bottom boilers.
The future trends for dry bottom boilers are positive. The demand for dry bottom boilers is expected to grow in the coming years, due to their increased efficiency and lower emissions.